Maybe it’s obvious -- but we’ve got the data here to prove it.
We pulled together data on reportable spills and lease operating expense (LOE) for firms of various sizes and found an extremely clear correlation between spills and LOE. We know, we know -- characteristics of individual wells and infrastructure can vary widely across the country.
We’ve shown here only data from Permian pure-plays to make sure we’re comparing apples to apples. While we’ve focused on the Permian, the same idea should hold everywhere: all else being equal, if you have fewer spills, you will have lower LOE.
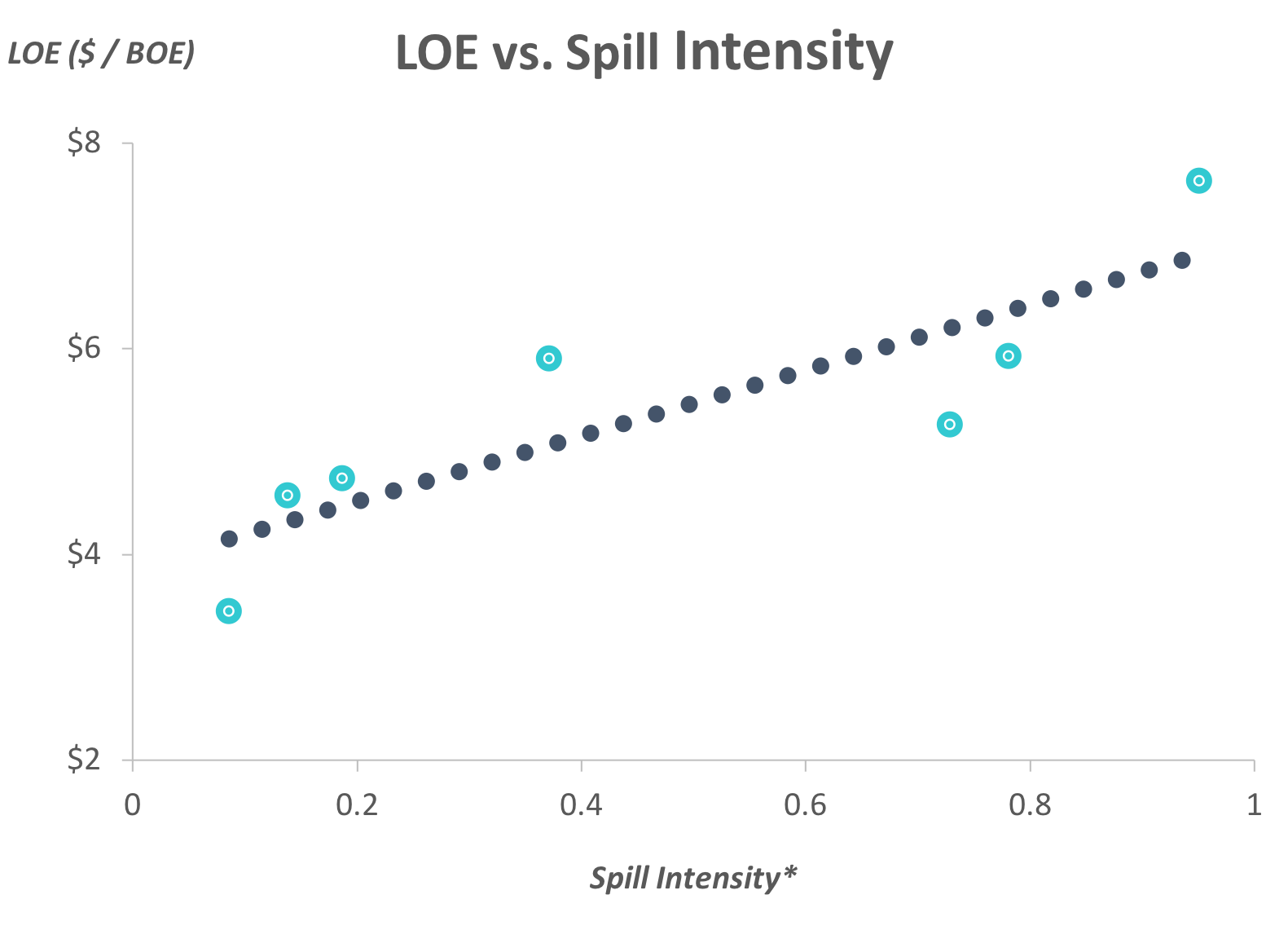
Why are we spilling?
Companies report that equipment failures/human error and corrosion are the major root causes of their largest spills. Training can help address these causes.
- Corrosion: A better trained operator will be able to recognize signs of corrosion earlier and better identify the common points of failure
- Equipment failures: Better trained operators maintain their equipment better and prevent breakdowns
- Human error: Well...this one’s kind of obvious. The better trained your operators are, the fewer mistakes they will make
While this data was useful, we thought it would be hard to create an effective training plan without more detail. So we looked at the data more closely in the Delaware Basin -- what were the most common spill sources?
-
Tanks: The number of tanks in the field and the corrosivity of stagnant produced fluids make tank corrosion inevitable. The best operators always get out of the truck, do their 360 walk around, and check behind the back tanks. Any new pools of liquid could be the beginning of a major tank failure
-
Piping: There are miles and miles of piping running within and across pads connecting all kinds of fluids to equipment. Fittings fail, poly wears down, steel corrodes. The operator that pays attention to the minor details on his piping saves the unnecessary downtime and spill
-
Pipeline: The volume released from a pipeline spill can be devastating given the time it takes to catch a leak from a trunkline underground. Great operators make sure the chemical pumps stay running at all times and prevent unnecessary water from flowing into oil lines
-
Valve: Valves left open or closed in the improper position are not a good look. The best operators know how every valve works, what purpose it serves, and can make repairs before a spill happens
-
Pump: Rotating machinery like pumps see a lot of wear and tear. Because pumps are connected to storage tanks, leaks from seals and fittings can cause high volume releases. Sometimes these leaks might be tough to catch ahead of time, but making sure the pumps are being properly maintained and watching for stresses on the fittings can reduce the risk of a large spill
-
Pressure vessels: Separators, heaters, knockouts...every vessel has at least one sight glass, and they are just about all designed to isolate the vessel when the glass breaks. Still, reportable spills continue to occur from broken sight glasses meaning a large number of folks aren’t performing the right maintenance or properly opening their gauge cocks
- Wellhead: Every rod lift well has a stuffing box with a bunch of different types of packing that needs to be checked and replaced regularly. Great operators understand the importance of keeping the stuffing box operating properly and are able to catch leaks before a major spill
We know you spend a lot of time thinking about spills. We do too, and we’d love to talk to you about training, spills and LOE.