Verify that each well is getting the right volume of gas injected
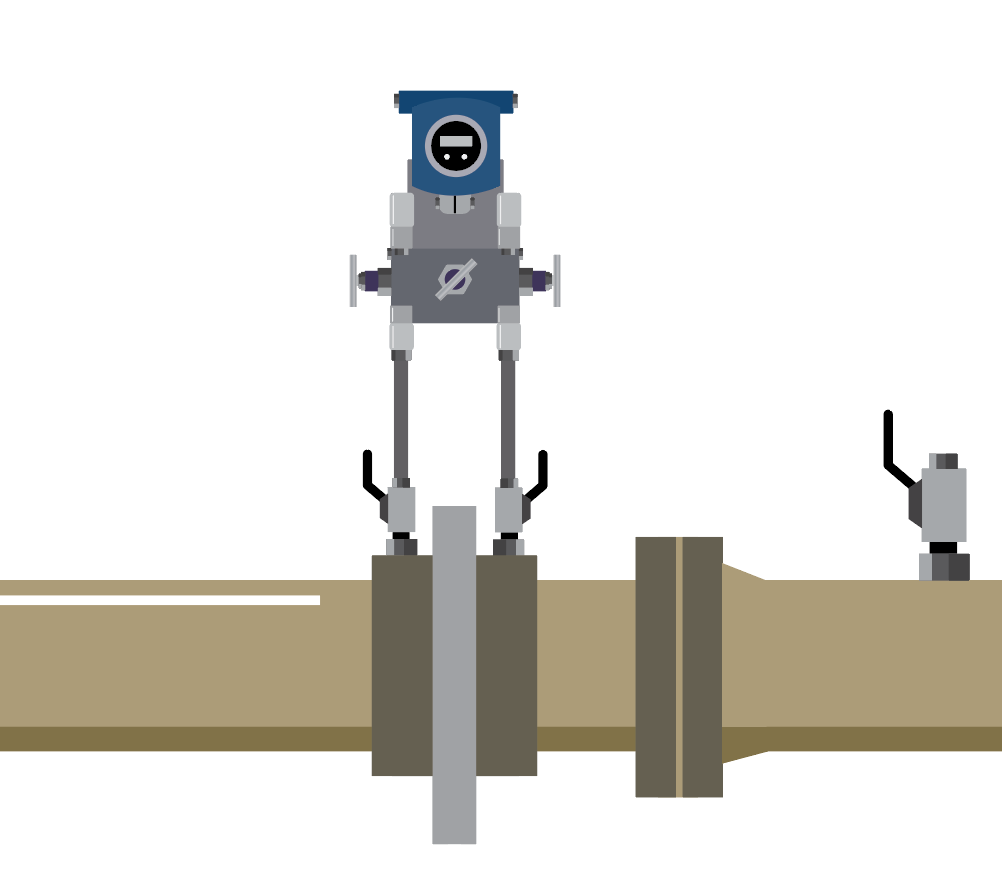
Adjusting the control valves
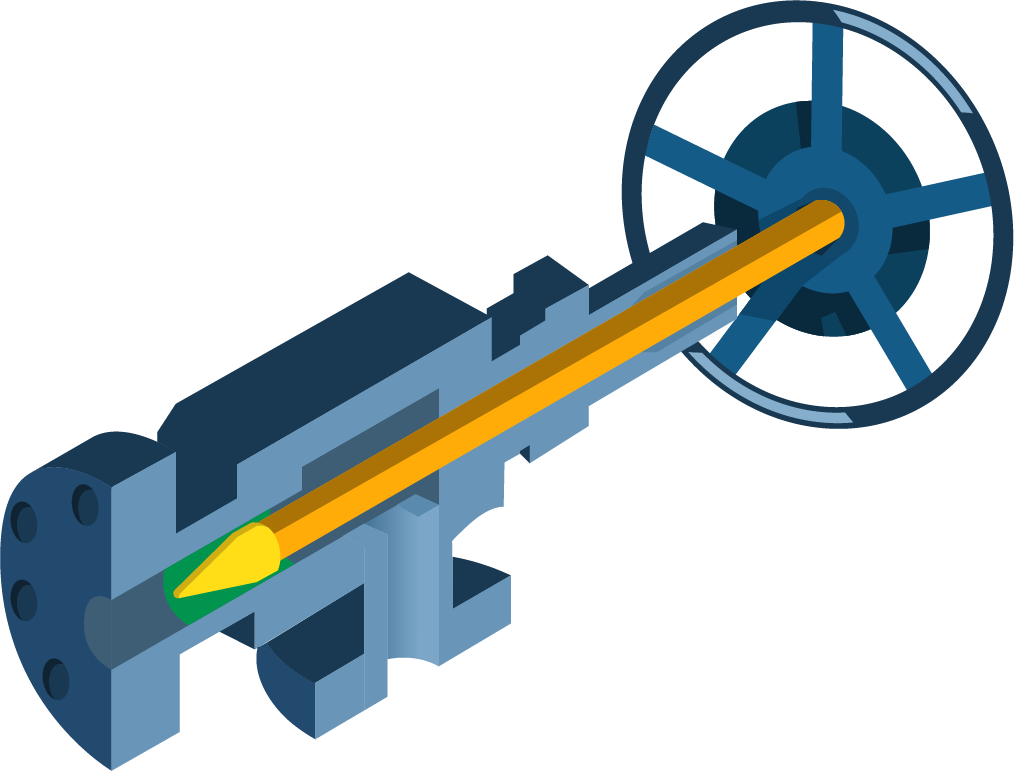
Adjusting the rate at the compressor
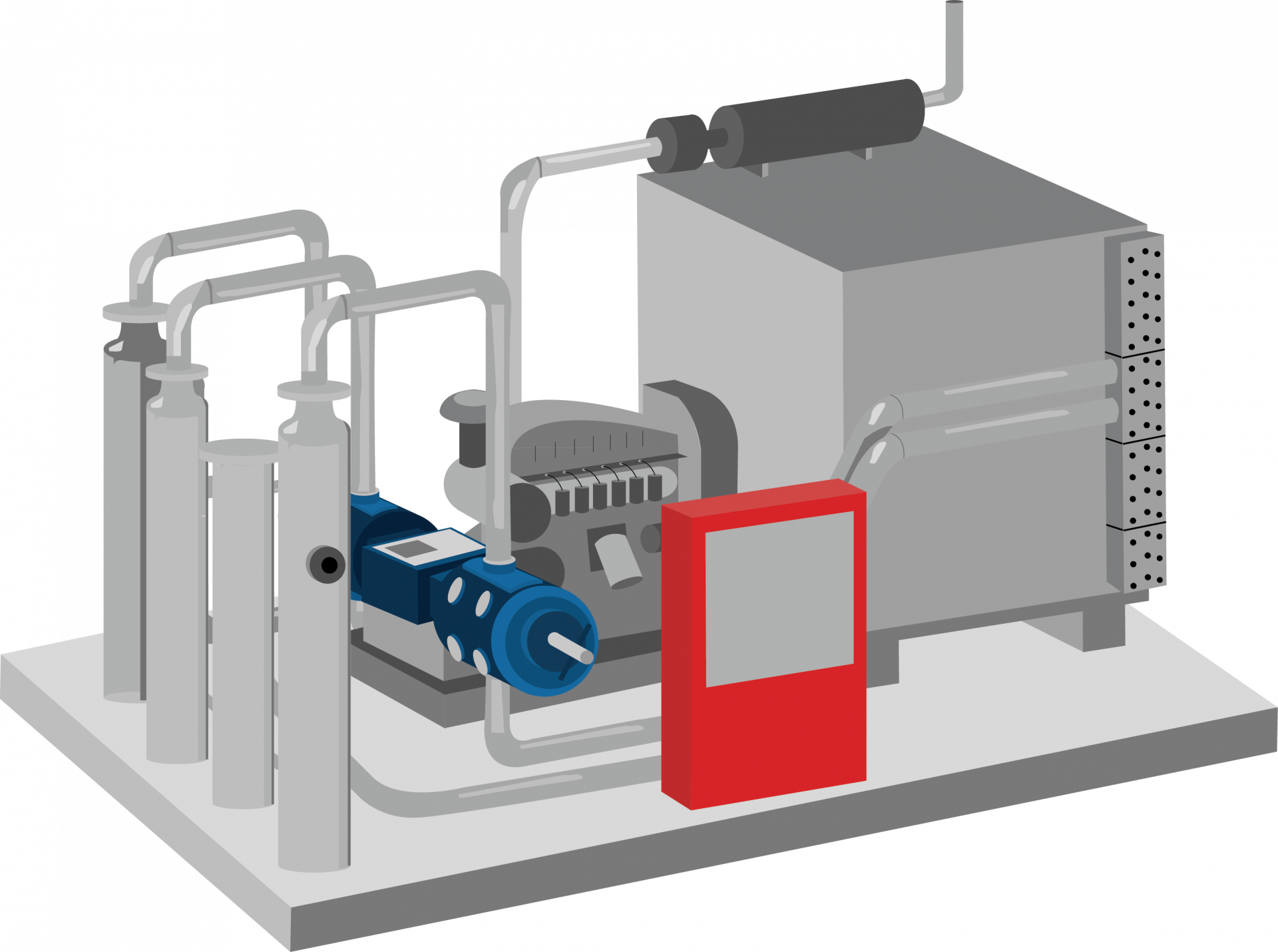
1. If running multiple compressors, you can shut each compressor down one at a time to see how much each compressor is moving. This can help identify which compressor might need adjustments made to it.
2. Increase / decrease the suction pressure. The throughput of the compressor is a function of suction pressure. A higher suction pressure will increase gas throughput.
3. Speed up or slow down the compressor. The compressor supplier will be able to give you the compressor’s operating range.
4. Check compressor valve temperatures with a temp gun. If one of the valves is running hotter than the rest, there may be a leaking valve that is lowering capacity.
Once you get the compressors and injection valves lined out and humming, you can really start optimizing for production.
Once you get the compressors and injection valves lined out and humming, you can really start optimizing for production.
Injecting only what the well needs
Every well is designed to have a certain amount of injection during unloading, but once the well starts also producing gas, the injection rate can often be lowered as the produced gas will help keep the well unloaded. As casing pressure decreases and lower valves are utilized, the injection rate can often be reduced.
A systematic way of prioritizing which wells are over-injecting or under-injecting is to check the amount of gas injected against the amount of fluid produced of all the wells on the pad. It is a good goal to aim to use roughly the same MCF of gas to lift one barrel of fluid out of each well on the pad. If you think a change is necessary, bump the rate on a well in 25 MCFD increments (adjusting rate at the compressor as well) and see if there’s a change in production over the next few days.
A systematic way of prioritizing which wells are over-injecting or under-injecting is to check the amount of gas injected against the amount of fluid produced of all the wells on the pad. It is a good goal to aim to use roughly the same MCF of gas to lift one barrel of fluid out of each well on the pad. If you think a change is necessary, bump the rate on a well in 25 MCFD increments (adjusting rate at the compressor as well) and see if there’s a change in production over the next few days.
Monitoring the recycle system
Lastly, the recycle system should be monitored as casing (and compressor discharge) pressures change over time. As the wells are drawn down casing pressures will typically decrease, which causes the compressors’ discharge pressures to also decrease. As the discharge pressure decreases, make sure the pilot on the recycle line gets adjusted to prevent over-injecting on any one well. This will also help prevent freezing across the valve in wintertime as pressure drop will be lower.
The goal is to minimize gas usage and compressor rental costs while keeping the well flowing at its maximum productivity as long as possible. With a little bit of patience and tweaking of the system, utilizing a few compressors to inject on a number of wells can be a great solution.