It’s that time of the year again - those of us in the oil patch are always wary of the first winter freeze. Even though we know it’s coming, it seems like a big freeze always happens during the holidays. Then we all get to dread the morning meeting after the break when we're asked why more winterization wasn't done ahead of time.
Last weekend we had another one of those freeze events. Data from BloombergNEF shows that last weekend Texas gas production dropped to levels not seen since last February’s Winter Storm Uri. We still have a few more months of winter and need to be sure to properly winterize to avoid these events, especially given our experience from the February 2021 outages.
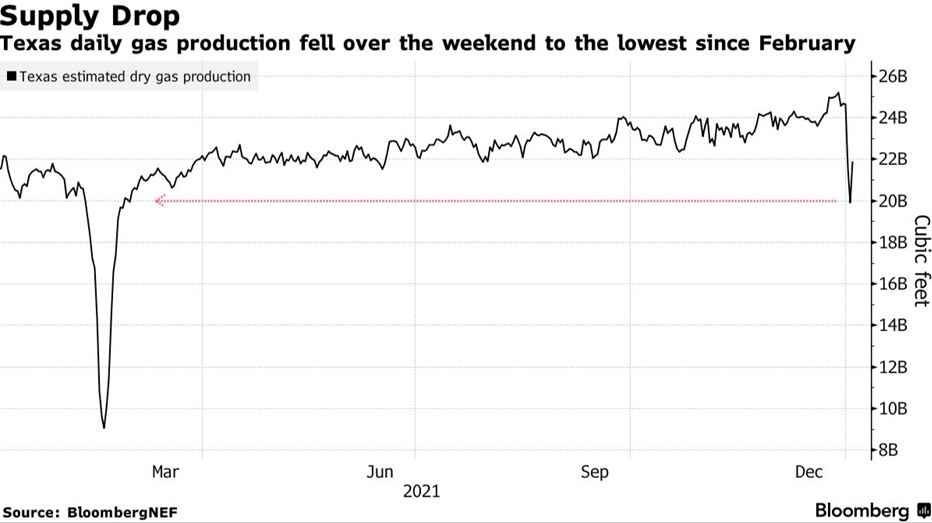
Maintaining Natural Gas Supply
The Federal Energy Regulatory Commission recently released their report detailing the causes of the February 2021 cold weather outages. What they found was that the second largest cause for the outages (after generation freezing issues) was natural gas fuel supply issues caused primarily by freezing at the well pad. Interestingly, a large portion of gas production declines in North and West Texas occurred before February 15th, when firm load shedding began. This means that many of the freezing issues in the field were occurring before power stations starting cutting off power.
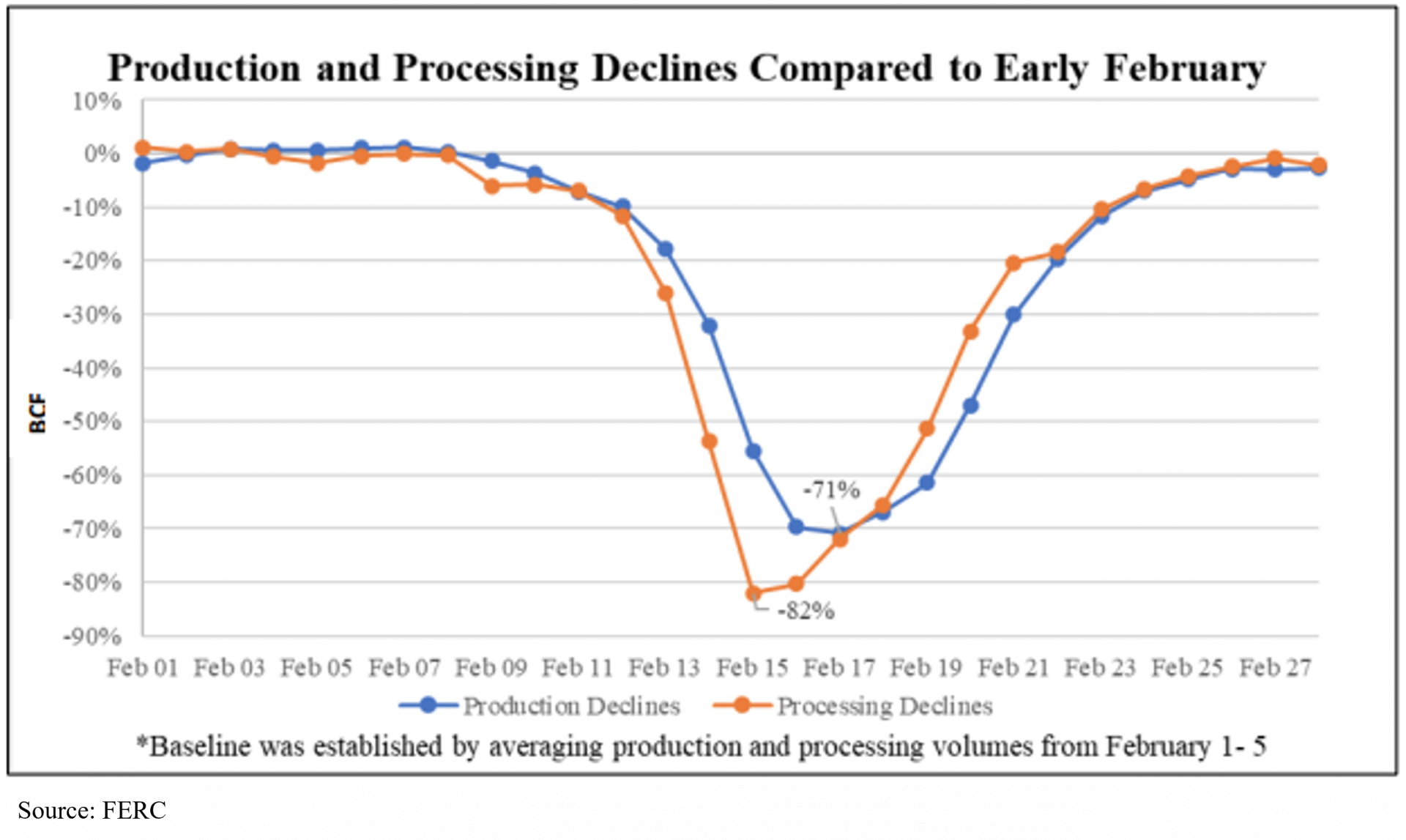
Based on these findings, one of the Key Recommendations from the FERC report is for companies to implement measures to directly protect vulnerable components against freezing. Many of the recommended measures can be quickly deployed, but operators need to understand which solutions are required under various conditions.
Many folks realize some mix of winterization solutions should be used, but there are a lot of misconceptions around how to implement them in the most effective way - it’s also just not always intuitive why or where equipment is freezing. Aside from misunderstanding the root cause of the freeze, part of the challenge is communicating best practices across the field. Each area has their way of doing things and they don’t all always work. However, using a digital platform can help companies overcome these challenges.
Many folks realize some mix of winterization solutions should be used, but there are a lot of misconceptions around how to implement them in the most effective way - it’s also just not always intuitive why or where equipment is freezing. Aside from misunderstanding the root cause of the freeze, part of the challenge is communicating best practices across the field. Each area has their way of doing things and they don’t all always work. However, using a digital platform can help companies overcome these challenges.
Wellsite LMS Winterization Training
Our operations training program provides many of the best practices we’ve gained over the years, some of which we discuss below. However, we understand that you know your field best. Which is why we can upload your specific company’s winterization checklists and best practices so your field staff can all access the same information. They can even reference this information on their phones while they are out in the field in real time!
Additionally, we can create interactive training modules with simulators and comprehension exams specifically for your own standard operating procedures and equipment setup. You can then ask your operators to work through these modules and track who all has completed the training.
In the case that you don’t have your own SOPs, you can use our off-the-shelf winterization training, which highlights the most common freeze locations on the pad, and primarily focuses on 3 main topics everyone should understand about freezing:
- Pressure drops: the standard rule of thumb is for every 100 psi of pressure drop the gas temperature will decrease 6-8°F. Identify the regulators and valves with the largest pressure drops to understand what will be the first freeze points.
- Ambient cooling: probably the most underestimated cause of freezing. Long runs of small diameter pipe that are exposed to Texas winds will see gas cooling much more dramatically than most people think. Process simulations show that a 1” line carrying supply gas for 30 feet can sometimes see extreme temperature drops even when the gas is coming off a separator that is over 100°F. Combine this initial ambient cooling with a 100+ psi pressure drop, and you’ll almost certainly start running into freezing issues if these lines aren’t insulated or have some strong heat trace.
- Hydrate formation: the most dangerous result of freezing. These ice-like solids are hydrocarbons trapped inside a crystal structure of frozen water. Interestingly enough, hydrate formation temperature is based on gas composition and typically occurs above 32°F, meaning hydrate plugs can form even above typical freezing temperatures. Methanol can be used to inhibit hydrates from forming, but typically will need to be atomized into the gas phase.
From our data we see that many field employees understand some of these topics, but usually not all. In order to limit the amount of shut-ins and production losses from freezing this year, we need to ensure every operator has the same understanding of freezing so the correct solutions get deployed.